3D printing adds new time-telling dimension

Watchmakers have spent more than two centuries perfecting the tourbillon mechanism, which brought unprecedented accuracy to time-telling, so the idea of an amateur making their own version from scratch might seem at odds with this hallmark of haute horlogerie.
Yet Christoph Laimer, a Swiss computer programmer, has done just that – he has 3D-printed the parts for his own tourbillon out of plastic, except for a few pins and screws. “It’s a design of my own. The mechanical principle is long known but the arrangement is new – it’s a reinvention,” he says.
Although Mr Laimer’s rendering is much larger than a conventional tourbillon and runs only for about 30 minutes before it must be rewound, it demonstrates the potential of a technology already widely used in jewelry making.

More
Financial Times
External linkWhile smartwatches and wearable technologies are sometimes cast as the cutting-edge of innovation in horology, watchmakers ranging from hobbyists and small independents to large Swiss houses are exploring the possibilities of 3D printing, also called “additive manufacturing”.
Through a process that forms objects layer by layer, it enables experimentation with new shapes and forms otherwise not possible by traditional machining techniques. This is expanding the boundaries of design and production in watchmaking, particularly with precious metals such as gold and silver, says Jeremy Hobbins, head of horology at Birmingham City University’s School of Jewelry.
“The way of modelling things means you can build things in a completely different way, such as hollow-form structures,” he says. “An advantage of laser sintering [a type of 3D printing] as opposed to casting is you’re able to produce a watch case out of solid metal but with a honeycomb interior, so it’s much lighter.”
3D printing also enables quick turnarounds and the ability to produce one-offs without needing to order parts or tools, making it a valuable tool for prototyping. Marques including Patek Philippe, Vacheron Constantin and TAG Heuer use it for this purpose.
New prices, accuracy challenges
Christian Selmoni, artistic director of Vacheron Constantin, says 3D printing is used for every new model and new case design. Over 10 years, he says, “it has proven to be a very important tool for us, as we can go quickly from computer renderings to a solid ‘volume’. It helps us a lot to judge the proportions and overall design of a watch case, for example.” But because they are not made of steel, 3D models do not have “the same definition” as the finished product.
Marc Walti, product director of TAG Heuer, concurs, saying 3D models do not have “the same aspect and light reflection as steel”. “In our field of activity, this is the best means to have a scale 1:1 prototype within a couple of hours – from 3D [computer-assisted] design to reality,” says Elie Bernheim, chief executive of Raymond Weil.
As such advantages favour small-scale producers, the technology is opening up entry points along the price scale for a new generation of watch designers and start-ups with novel or unorthodox ideas.
Industry figures add that 3D printing technologies are not yet accurate enough for movements – the complex beating heart of a mechanical timepiece. Items made with 3D technology are typically non-moving parts such as dials, cases and straps.
Creative marketing
Over the past couple of years a handful of chronometric ventures using 3D printing have sought internet crowdfunding. These have ranged from a watch printed out of a wood-like composite material to a brand that allows buyers to customise colours, patterns and cut-out initials on a flexible nylon strap, though not all are successful.
One company in the small but growing field of watch “micro-brands” is ALB (Atelier le Brézéguet). The two-man French outfit makes colourful and three-dimensional dials – one represents a countryside landscape, another a sky – that are mounted on movements manufactured by ETA, a company that is part of the Swatch Group.
“We decided to use 3D printing not for trendy reasons but because it was the only way to do something different from what we could find on the market,” says co-founder Simon-Pierre Delord. “We create a frame that’s like a painting.”
Despite only initially intending to make some watches for friends, the pair now make a handful each month to order, with price tags of €1,500 and €2,500 (CHF1,647 and CHF2,744). They hope to sell some items in shops before the end of the year.
Going big
In a profession that cleaves to its artisanal traditions, there are also signs that some bigger and longer-established horologists are starting to harness additive manufacturing for larger-scale production.
Mappin & Webb, an English silversmith that once made earrings for Marie Antoinette and traces its roots to 1775, has for several years produced bespoke jewelry such as wedding rings through 3D printing. This summer it will launch its first watches with cases made that way – two pieces resurrected from its archives “with a slightly modern twist”, says Elizabeth Galton, the company’s creative director.
One is the Austen for women, inspired by 1920s dress watches worn either on a silk strap or hung from a lapel, retailing at £900. The additive process helped with modifications: its Art Deco design was “technically quite a challenge as it’s quite slim with a curve”, Ms Galton says.
She does not see a cultural clash between the old and the new techniques: “[3D printing] has almost become a way of life, which makes our workshop a lot more efficient and does complement those hand and artisanal skills.”
Limits of ‘addictive manufacturing’?
But some houses are “scared” of using additive manufacturing for end-products in case they lose their handcrafted brand value, according to Michael Sorkin of Formlabs, which supplies desktop 3D printers to professional designers, dentists and jewelers, as well as watch companies.
Mr Sorkin says that despite the excitement surrounding the technology, or perhaps because of the hype, the full potential of the technology risks not being realised in watchmaking. “There’s a danger of 3D printing being used as a cool gimmick,” he says.
Other limitations of the present technology include tolerances, or the degree of deviation from a parameter of accuracy. “If you want to do an assembly of a watch [movement], it could be OK at 0.1mm, but normally you need to be under 0.1mm,” says Simon-Pierre Delord of ALB, who adds that his parts take about five attempts on average to get right.
For now, consumer interest appears limited to enthusiasts who are keen on the capabilities of the technology, according to Robert-Jan Broer, who runs the Fratello Watches blog.
Yet he says additive manufacturing could take off where it offers lower costs and the ability to make uncommon designs, particularly in the case of smaller producers.
“Price wise, some micro-brands are really interesting as they tend to stay below €1,000 for a mechanical watch [whereas] with the established brands it’s more difficult to find one below €2,000 these days,” he says.
Copyright The Financial Times Limited 2016
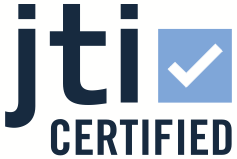
In compliance with the JTI standards
More: SWI swissinfo.ch certified by the Journalism Trust Initiative
You can find an overview of ongoing debates with our journalists here. Please join us!
If you want to start a conversation about a topic raised in this article or want to report factual errors, email us at english@swissinfo.ch.