Lego faces uphill battle to build new markets
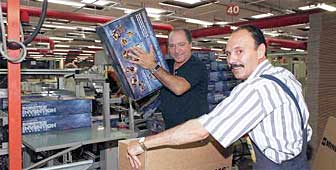
Lego has long been a household name, but the company's legendary building blocks are finding it difficult to compete with the thrills offered by state-of-the-art computer games. Change is underway, though, at Lego's Swiss operations.
Unlike many toy companies, which outsource production to the developing world, where labour is cheap, Lego’s European production headquarters are in one of the most expensive locations in Europe – Baar in canton Zug.
Although based in the Danish town of Billund, Lego chose to locate its factory in Baar both because the canton has very low tax rates, and because those famous building blocks actually require little labour to produce.
“The moulding process we use at Lego is highly automated, and hence not labour intensive,” explains Werner Häfliger, the director of Lego Switzerland.
“That means that given the high salaries in this country, we are able to operate at affordable rates. Also, by having our production in Switzerland, we can take advantage of a skilled labour force that can deal with the technology and complexity involved in the making of our products.”
The Baar plant produces the larger Lego bricks for pre-schoolers (called “Duplo”), as well as a line called Lego Technic.
The factory stands out among its grey neighbours, thanks to what must be the largest cement Lego brick in the world, which stands outside the entrance to the building.
What really distinguishes Lego Switzerland, though, is perhaps its multi-ethnic workforce. It has 27 nationalities amongst its workers, and Häfliger has no doubt that the mix of languages, cultures and religions makes for a rich working environment.
“It’s a definite advantage for both the employees and the management,” he says, leaning against a large machine on which a rudimentary smiling face has been fashioned out of colourful pieces of plastic.
“The workers themselves are forced to deal with many ethnic backgrounds on a daily basis, and it’s good for the Swiss management, too. You know, our country isn’t known for being very open and liberal.
“But here we have a nice mix and we know full well that there are very few Swiss people who would be willing to do this kind of job.”
But life at the plant isn’t always trouble free. “Occasionally someone will refuse to work in another team because of another member’s ethnic background,” says Häfliger. “Until now, we have managed to avoid significant conflicts.”
For Lego’s top management, conflict on the shop floor is the least of their worries. Lego’s balance sheet is not looking altogether healthy.
The company estimates it will make a loss this year, and accordingly jobs will have to be cut worldwide as part of ongoing restructuring.
The Swiss management declined to say how many employees in Switzerland would face the sack, but it admitted that Lego products are losing out to new state-of-art toys
“‘Pokemon’, computer games and even kickboards are catching kids’ fancies more than time-consuming building bricks,” Häfliger says.
“Kids are under a lot of pressure time-wise – with their timetables full of schoolwork and sporting activities – so, although our toys are high quality, the masses are going for instant-gratification leisure activities.”
Lego plans to bring out a number of high-tech products in the coming year, including a “Lego and Steven Spielberg Moviemaker Set” which won prizes for interactive entertainment at the BAFTA awards (British Film & Television Arts) in the UK.
Lego says it is also determined to maintain its record as a company which treats its employees well. “Lego takes its employees very seriously,” explains Häfliger.
Nearby is the financial services department. One corner has been decorated by employees and resembles something of a desert oasis, with plastic palm trees and colourful children’s drawings.
“Our employees are our best advisors, and to get the best input from them, we have developed a tool called ‘Dream Outs’. Using them, people can define problem areas and rally a group of colleagues to find a solution.”
In Baar, two “Dream Outs” are on the cards. The first is called Open Factories 2001, and aims to make certain parts of the production process safe enough for children to walk through and see how their toys are made.
Perhaps more exceptional is the other “Dream Out”, which will allow employees to bring their children to work during office hours.
Most Lego workers are part of double-income families and Lego has had plenty of enquiries from parents wanting to bring their children to work.
It is an unusual step, but one which Lego believes may have great potential. The company says: “Children are our natural role models” and it aims “To nurture the child in each of us”.
Having a factory full of children will certainly test the sincerity of those mottoes.
by Juliet Linley
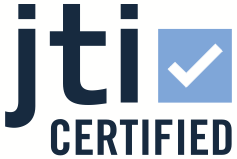
In compliance with the JTI standards
More: SWI swissinfo.ch certified by the Journalism Trust Initiative
You can find an overview of ongoing debates with our journalists here . Please join us!
If you want to start a conversation about a topic raised in this article or want to report factual errors, email us at english@swissinfo.ch.