Metallic glass could help fix broken bones
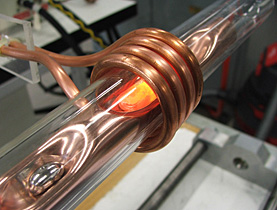
While corrosion is usually considered undesirable by engineers, Swiss scientists say implants that "biocorrode" could play a major role in the future of medicine.
Mending broken bones for example with so-called metallic glass would not only do away with the need for implant-removal surgery, but also circumvent the long-term negative effects of permanent implants.
“Materials researchers have been trying to develop biodegradable implants for osteosynthesis and cardiovascular intervention for several years,” Jörg Löffler, professor of metal physics and technology at the Federal Institute of Technology in Zurich (ETH), told swissinfo.ch.
Osteosynthesis is a surgical procedure that stabilises and joins the ends of fractured or broken bones by mechanical devices such as stainless steel or titanium plates, pins, rods, wires or screws.
“The idea is basically that the implants stay in the body for a certain amount of time and then dissolve after performing their task,” he said, adding that the material needed to be adjusted according to the application.
“With a stent [a sort of tube often used in angioplasty], the material should degrade after maybe six months – until the artery has stabilised. In bone surgery, the implant should stabilise the bones for as long as they need to heal and then dissolve in the body so that surgical removal is not necessary.”
No bubbles
One of the problems with this so-called internal fixation – as opposed to external fixation using splints and casts – is that once the bones have healed, the metal parts have to be removed via further surgery.
Implants made of magnesium-based alloys are proving particularly promising. These light metals are mechanically stable and ductile, and degrade quickly and completely by releasing ions which are tolerated by the body.
There is however one major drawback to magnesium alloys, which Löffler said had until now prevented their use for biodegradable implants in osteosynthesis.
“When they dissolve, they produce magnesium hydroxide and more importantly hydrogen, so gas bubbles are produced in the tissue around the magnesium implants. These can hinder bone growth and the healing process. They may also lead to infection.”
Researchers led by Löffler have now eliminated these side-effects by producing an innovative magnesium-zinc-calcium alloy in the form of a metallic glass which is biocompatible and degrades quite differently.
“In animal tests there were no observable gas bubbles for this magnesium-based glass,” he said. “We cannot completely exclude that there’s no hydrogen, but we do not clinically observe it anymore.”
Potential
The key to the discovery is the cooling process.
Metallic glasses are produced by rapid quenching, or cooling, of the molten material. The speed of the cooling process prevents the atoms from adopting the crystal structure found in traditional metals. As a result, metallic glasses have an amorphous structure like that of window glass – although they look like metals.
Thanks to this procedure, the researchers can add much more zinc to the magnesium than is possible with conventional alloys.
The alloy developed by Löffler’s doctoral student Bruno Zberg contains up to 35 per cent zinc and five per cent calcium atoms – the rest is made up of magnesium. A crystalline magnesium-zinc alloy can contain a maximum of 2.4 per cent zinc atoms. If the percentage is higher, an undesired crystalline phase precipitates in the magnesium matrix.
The major advantage of a high percentage of zinc is that it fundamentally changes the corrosion of the magnesium: clinical tests with small amounts of the new magnesium-zinc-calcium alloy showed no hydrogen evolution.
This means that this new alloy, in the form of a metallic glass, has considerable potential as a non-harmful bone implant material.
As for realising this potential, Löffler says he is hopeful, but admits that the deployment of this new material in for example bone implants “will still take a few more years, as further clinical tests need to be performed to demonstrate beyond any doubt that our new material fulfils all necessary requirements”.
Thomas Stephens, swissinfo.ch
Metallic glass is a hot topic in the field of materials science. Only since the early 1990s have metallic glasses been produced in larger dimensions and used as engineering material in the form of “bulk metallic glasses”, according to Löffler.
Since then laboratories have been searching intensively for applications for such glasses, which have several advantages over traditional metals. They are much more elastic than crystalline materials and demonstrate a strength that is two to three times higher. These properties would be valuable in bone implants, as metallic glass parts could carry out the same function as their traditional crystalline counterparts but be much smaller.
However, metallic glasses also have some disadvantages: their plasticity is not as high as that of normal metals; and, depending on the composition of the alloy, individual components can often only be produced in thicknesses of a few millimetres to centimetres (otherwise they cannot be cooled quickly enough and a crystal structure forms). For this reason metallic glasses are mostly used in filigree devices, for example in the field of sensory applications and microtechnology.
The magnesium-zinc-calcium alloy developed by Zberg can be produced in a thickness of up to five millimetres.
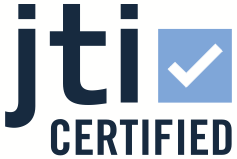
In compliance with the JTI standards
More: SWI swissinfo.ch certified by the Journalism Trust Initiative
You can find an overview of ongoing debates with our journalists here. Please join us!
If you want to start a conversation about a topic raised in this article or want to report factual errors, email us at english@swissinfo.ch.